
When it comes to energy efficiency, innovation is key in any initiative to maximise the ratio of energy-savings to system implementation cost.
In this respect, Airius, an energy-efficiency expert based in region of France Loire-Atlantique, has for more than eight years been offering to businesses and local authorities an innovative solution based on the principle of thermal destratification.
What is thermal destratification?
The innovative principle at the heart of thermal destratification consists of drawing hot air from a landing (floor) or storage area and reinjecting it below where it was drawn from. This mixing system reduces the energy needed to heat a room (via a classic heating system) by focusing on redirecting naturally heated air (naturally closest to the ceiling) or device-heated air (primarily seen in warehouses).

Thermal destratification produces energy savings of some 25% to 30%.
Outfitting of ArcelorMittal warehouses
In 2018 Airius undertook a number of warehouse outfitting projects for ArcelorMittal, including Mardyck in northern France.
As the biggest steel producer in the world with 96.42 million metric tons produced in 2018, ArcelorMittal Group is vulnerable to metal fragility due to humidity causing it to deteriorate rapidly. It is therefore necessary for the Group to, at any cost, prevent its steel from reaching dew point, which is the temperature at which the surrounding air becomes saturated.
It is to counteract this vulnerability and to prevent any risk of metal deterioration that a number of thermal destratification projects have been set up.
The impressively large dimensions of the warehouses (20m high, 150m long, 50m wide on average) showcase the effectiveness of those destratification projects.
For each project, a 7-year Energy Savings Contract (ESC) has been defined including a binding commitment to reduce energy use by 20%. Each project is self-funded by the savings achieved each year.
Project phases – The Mardyck warehouse as example
Phase 1 of the project consisted of setting up Enless Wireless ambient temperature and humidity sensors in various places at the warehouse, defined by homogeneous climatic conditions. Sensors were also placed on the ground floor, the ceiling, and near the destratifiers.

Critical temperature and humidity thresholds were defined, which correspond to dew points.
To enable accurate tracking, Enless Wireless pulse transmitters were also installed and connected to electricity and gas meters at the site to monitor changes in energy consumption on an approximately weekly basis. This installation also enabled detailed measurement of the energy consumption of each Group department so as to more accurately apportion overheads.
Phase 2 of the project consisted of Airius technical staff setting up destratificators at the highest parts of the warehouse. The job of the destratificators is to push hot air lingering at the ceiling towards the floor, without being noisy or creating drafts. This makes the temperatures at the ceilings uniform, even in very tight spaces, and the dew point is never reached.

Phase 3 of the project concerns the monitoring of ambient temperature and humidity data as well as the data uploaded by the Enless Wireless Pulse transmitters connected to the meters. The ambient data is sent every ten minutes on average (five minutes in the most sensitive zones) by the Enless Wireless transmitters to the Lacroix Sofrel PCWin2 controller. The pushed data is then analysed and monitored on a daily basis by Airius management teams via the robot’s supervising software.
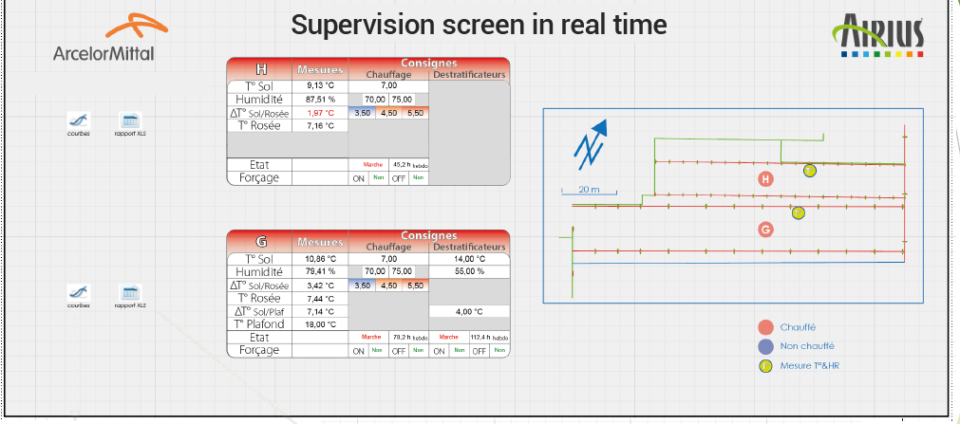
What other projects are in progress?
Outfitting of ArcelorMittal French sites of Nantes – Basse-Indre (10 Enless Wireless ambient temperature and humidity transmitters) and Dunkirk (12 Enless Wireless contact sensors to control the opening and closing of destratification doors) are also in progress.
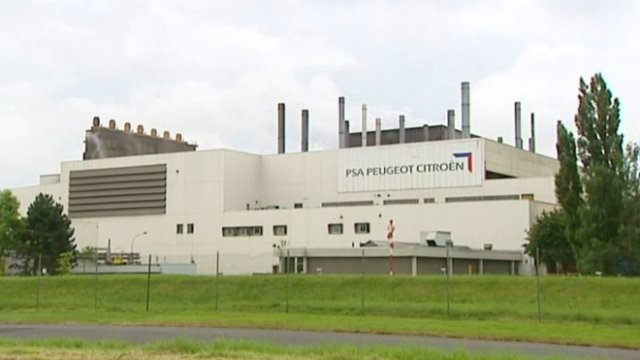
A destratification project has also been launched for PSA Automotive Group and the PSA plant in Charleville. It produced an order for the first 12 Enless radio transmitters installed on warehouse floor and ceiling. The Phase 1 test which was recently completed consisted of fully outfitting a test environment and comparing the test results against the readings taken by a reference workshop not equipped with the destratification system. Initial results show a positive trend.
To learn more about what Airius does, go to www.airius.co.uk/.
Click on the icons below to post this article on social networks >>>